
A commercial construction project is more than just blueprints and permits—it’s a carefully orchestrated process where efficiency, quality, and cost control must align. Yet, too often, projects run over budget, fall behind schedule, or fail to meet the intended vision. The key to avoiding these pitfalls isn’t simply spending more or cutting corners—it’s about strategic planning, assembling the right team, and making informed decisions at every stage.
Whether you’re developing a new office space, renovating a retail property, or expanding an industrial facility, optimizing your construction strategy can mean the difference between a smooth, cost-effective build and a drawn-out, over-budget nightmare. Below are advanced-level strategies to maximize efficiency without compromising quality.
Start with a Pre-Construction Plan—Don’t Skip the Details
Rushing into construction without a solid plan is one of the biggest reasons projects face delays and unexpected costs. The pre-construction phase is where you set the foundation for success. This includes feasibility studies, budgeting, risk assessments, and clear scope definitions.
A strong pre-construction plan should include:
A realistic timeline with contingencies for potential delays.
A fully detailed budget that accounts for materials, labor, soft costs, and contingencies.
Permit and zoning research to avoid legal bottlenecks.
A project scope document outlining exactly what is included (and what is not).
The more thorough this phase is, the smoother the actual construction process will be.
Hire a Construction Manager Early—Not Just a Contractor
Many businesses go straight to hiring a general contractor, assuming they will oversee everything. While contractors are essential, they primarily focus on executing the build, not overall strategy. This is why hiring a construction manager (CM) early can be a game-changer.
A CM acts as your advocate, ensuring that design, budget, and timeline stay aligned. They help:
Review contractor bids to prevent overpricing.
Negotiate better material and labor costs.
Spot potential issues before they cause costly rework.
Manage scheduling conflicts between subcontractors.
Bringing a CM into the project before design begins ensures that real-world cost and feasibility considerations are factored in early, rather than making costly corrections later.
Use Design-Build Instead of Design-Bid-Build
Traditional construction follows a design-bid-build model, where an architect designs the project, and then contractors bid to build it. The problem? This creates a disconnect between design and cost, often leading to budget overruns and delays.
Instead, the design-build approach brings architects, engineers, and builders together from the start, reducing miscommunication and ensuring a more cost-efficient and faster project. Benefits of design-build include:
Faster project timelines since design and construction overlap.
Cost control from the start because builders provide input on materials and labor costs.
Fewer design errors since engineers and contractors collaborate early.
For projects where time and budget are major concerns, a design-build approach often delivers better results.
Choose the Right Delivery Method (Not Just the Cheapest One)
Selecting the right construction delivery method is one of the most important decisions you’ll make. The wrong method can cause delays, budget issues, and coordination headaches.
Key delivery models:
General Contracting (GC): Best when the project is straightforward and well-defined.
Construction Management at Risk (CMAR): Ideal for complex projects needing flexibility and cost control.
Design-Build: Recommended when speed and cost certainty are priorities.
Integrated Project Delivery (IPD): The most collaborative, suited for highly complex projects requiring innovation.
Each method comes with different risk levels and cost structures. Carefully evaluating which approach aligns with your budget, timeline, and risk tolerance can prevent major problems down the road.
Invest in Value Engineering—But Be Strategic
Value engineering isn’t just about cutting costs—it’s about maximizing value per dollar spent. The goal is to identify alternative materials, methods, or designs that reduce costs without sacrificing quality.
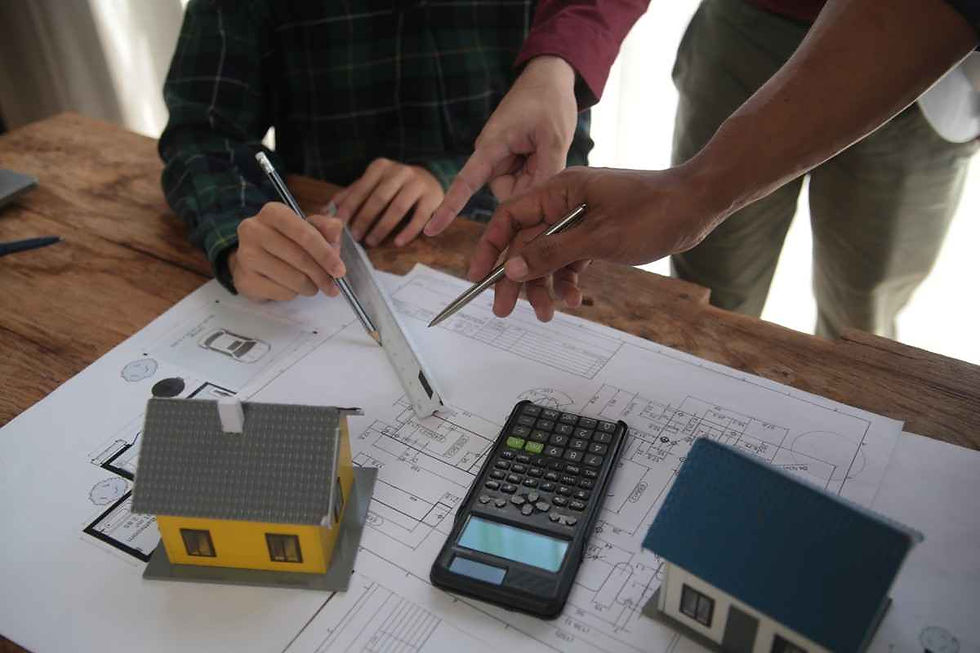
Examples include:
Using pre-fabricated components to reduce labor time.
Revisiting material choices (e.g., swapping stone for high-quality composites).
Reassessing structural requirements to avoid over-engineering.
Optimizing HVAC and electrical layouts to lower long-term operational costs.
However, poorly executed value engineering can backfire. Cutting costs on foundational materials or skilled labor can lead to higher repair and maintenance costs later. The key is strategic trade-offs—reducing unnecessary expenses while maintaining performance and longevity.
Manage Permits and Compliance Proactively
Permit delays can halt a project before it even starts. Many companies underestimate how long it takes to secure zoning approvals, environmental clearances, and building permits. A proactive approach can save months of unnecessary delays.
Best practices include:
Engage permit expeditors to navigate complex approvals faster.
Start the permit process early, often during design rather than after.
Ensure all documentation is complete before submission to avoid rejection.
Maintain compliance throughout the project to prevent stop-work orders.
Delays due to missing permits can add thousands of dollars in holding costs and disrupt the entire timeline. Staying ahead of compliance requirements prevents expensive headaches.
Reduce Change Orders with a Detailed Scope of Work
Change orders are one of the biggest budget killers in construction. Many projects see costs spiral because of unclear project scopes that lead to mid-construction modifications.
A well-defined Scope of Work (SOW) should:
Outline exact materials, dimensions, and construction methods.
Define responsibility for unexpected site conditions.
Specify cost thresholds for approved modifications.
Change orders should only happen when truly necessary—not because of poor planning. Detailed upfront coordination between designers, builders, and owners reduces costly surprises.
Track Costs and Schedule in Real Time
Even the best-planned projects can go off track without real-time monitoring. Many companies still rely on outdated reporting methods that only highlight cost overruns and delays after they’ve already happened.
Investing in construction project management software allows for:
Live cost tracking to flag overages before they get out of hand.
Automated schedule adjustments to prevent cascading delays.
Digital document sharing to improve team coordination.
By catching issues early, real-time tracking prevents minor problems from turning into major financial setbacks.
Saving time and money in construction doesn’t mean cutting corners—it means making strategic decisions that align with the project’s goals. From choosing the right team and delivery method to leveraging value engineering and proactive compliance, the right approach can deliver a project on budget, on time, and without sacrificing quality.
By taking a structured, well-planned approach, businesses can navigate commercial construction efficiently, avoiding the common pitfalls that derail projects. Whether you're building new or renovating existing space, these strategies ensure that every dollar spent contributes to long-term success